You might notice as we continue this post that it isn’t the coat I mentioned in my review post.
No, it is not.
A new dress was required to wear to a wedding (weddings are great excuses for new ANYTHINGS aren’t they?!)…and I got offered some free fabric.
One must never say no to free fabric.
So I made a new dress!
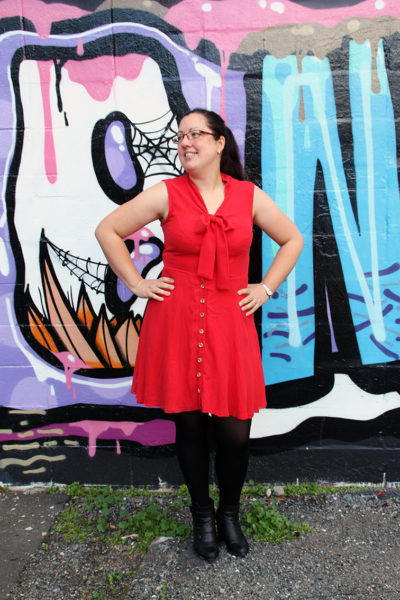
This pattern comes as a dress or blouse with front and back darts, lightly gathered sleeve head, quarter circle skirt or peplum, and a neck bow. There is also a skirt option with button down front quarter circle and shaped waistband.
The bodice is underlined and the skirt lined in a red chiffon for extra floatyness which I know will sound incredibly and luxuriously over the top and it is but it’s a whole other story as to how that happened!
So back to the dress…don’t be afraid of naughty slippery fabrics. To counter the sheerness of georgette I underlined the bodice with the chiffon. Keep both pieces together by basting within the seam allowance…or be lazy like me and use lots of ultra fine pins to keep everything in check.
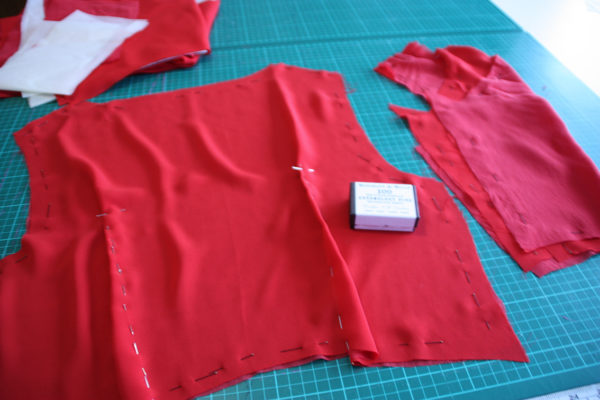
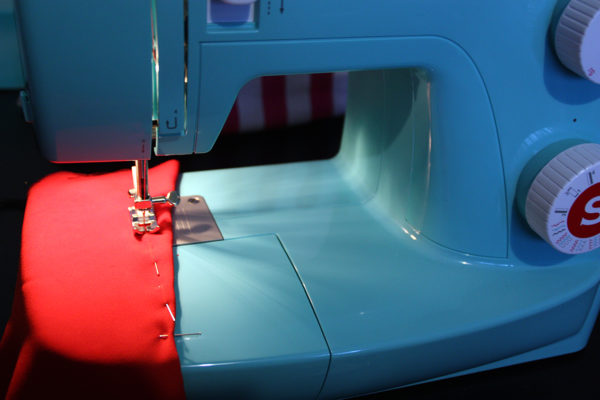
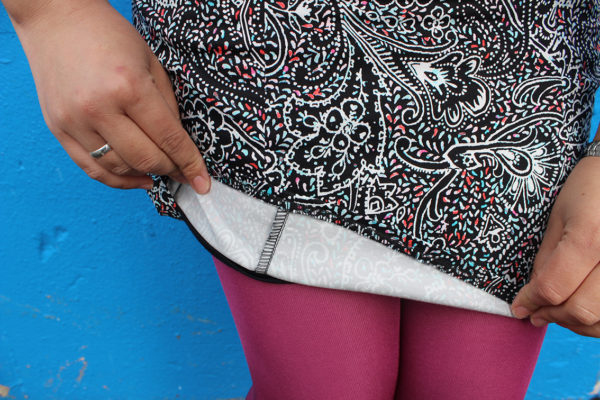
Papercut patterns have a seam allowance of 1cm so I began by pinning my pieces wrong sides together. Now it will feel weird to sew looking at the right side of the fabric but trust me!
I sewed my first line of stitching at 0.5cm. It’s was a little tricky because the width of the machine foot is larger than that so I checked with my sewing guide and saw that 0.5cm lined up perfectly with the point of the foot.
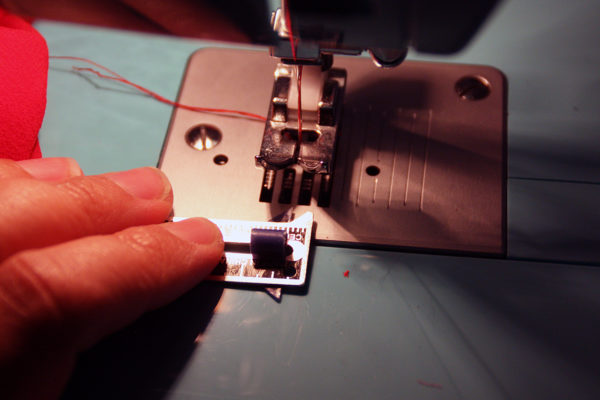
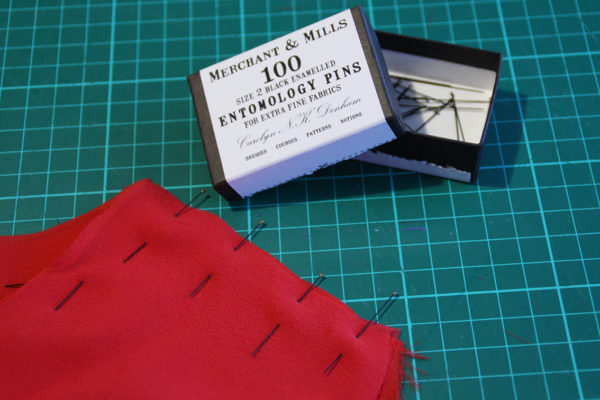
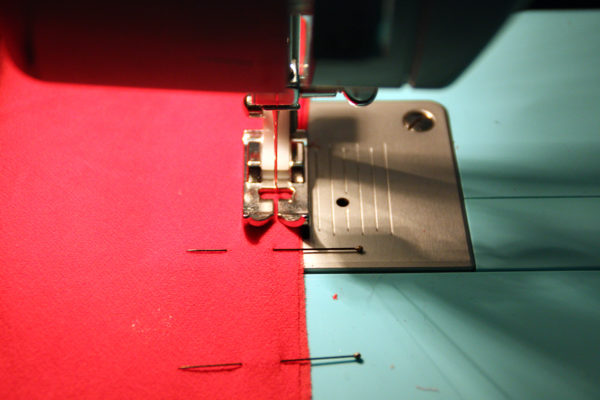
Next I trimmed 0.2 cm off the seam allowance.
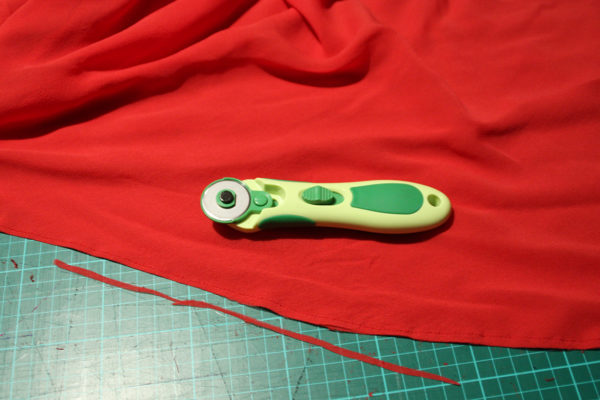
Next fold the fabric right sides together along the seam. Press the seam flat with the stitching on the folded edge.
Pin layers together along the pressed edge.
Sew your second line of stitching at 0.5cm, encasing the original seam allowance edge inside the line of stitching.
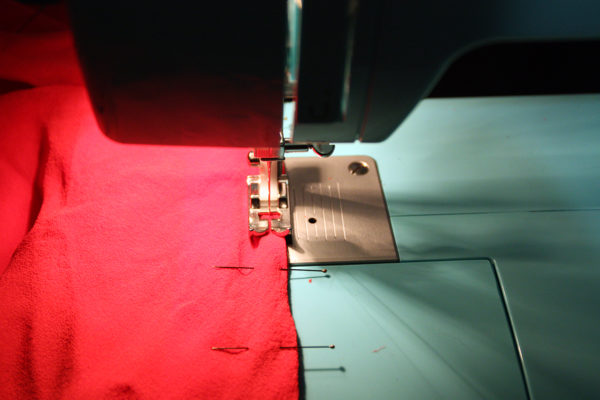
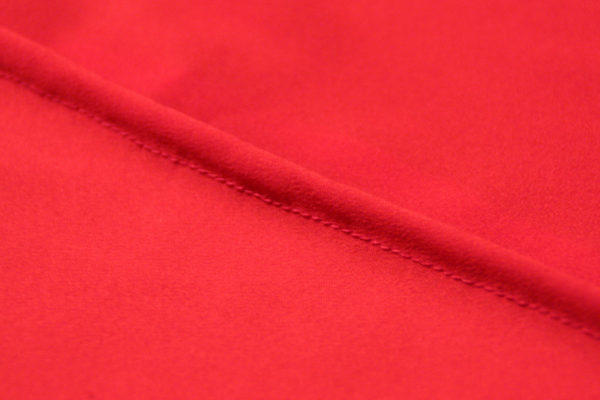
If your pattern has a different seam allowance then you’ll need to adjust the numbers above. For example, many commercial patterns use 1.5cm – Sew your first seam at 1cm, then trim down to 0.3cm. Sew your second seam at 0.5cm. As long as your first and second seam allowance amounts add up to your total seam allowance (1cm + 0.5cm = 1.5cm) then you are good!
Phew! French seams can be time consuming. Time for a supervisor break…
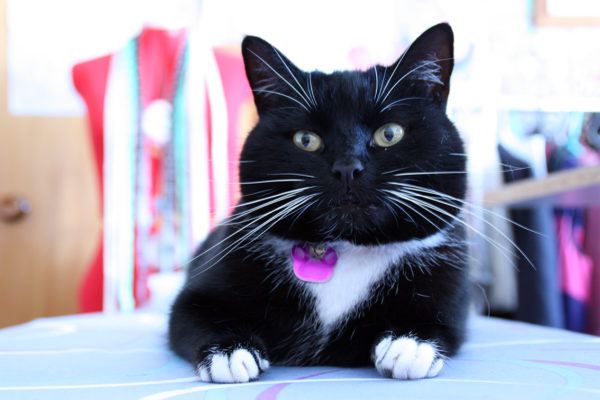
I make all my bias tape from scratch using a Clover bias tape maker. It looks a bit fiddly but it’s easy peasy and you can have bias in any colour or pattern you want!
Another trick I’ll share while we’re at it: I keep all the little slips of paper I get with any sewing tool in a folder so that I can refer to them later. Everything from the bias tape maker instructions (with handy table of cut fabric widths) to complicated sewing machine feet set up (I’m looking at you pleating foot!), and even interface fusing instructions. Super nerdy but super useful.
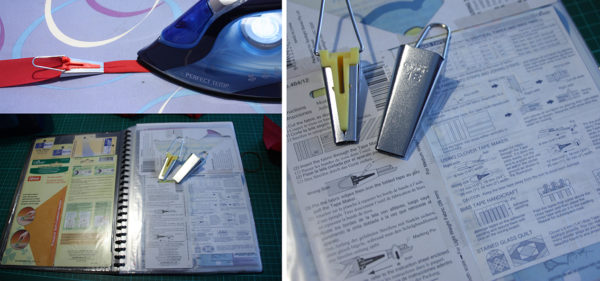
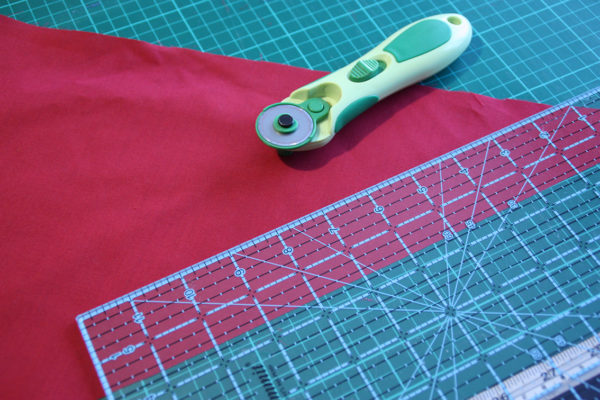
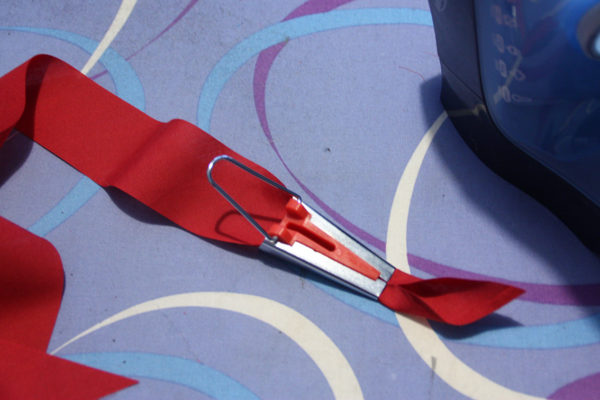
Click on the photo below for a little demo video.
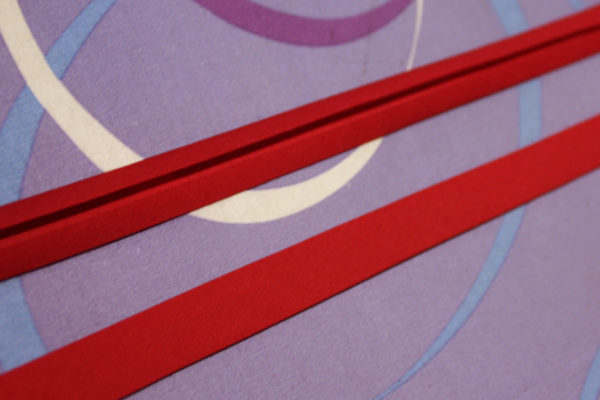
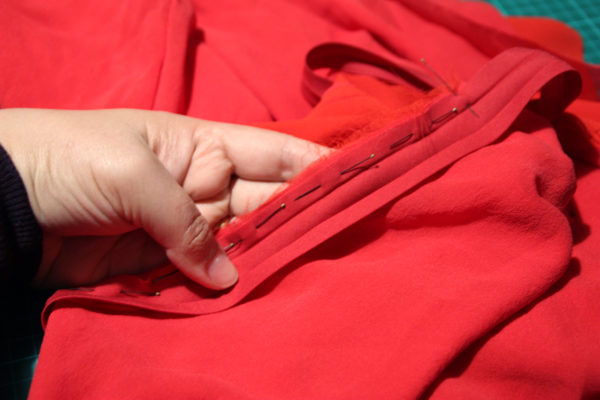
Stitch the bias tape to the bodice in the fold all the way around the armhole.
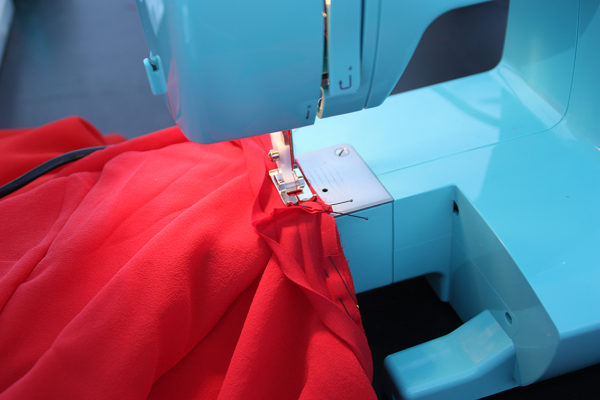
If you are patient (unlike me) you could hand-stitch the inside edge of the bias tape to the underlining for an invisible finish. I decided to top stitch close to the inside edge of the folded bias tape.
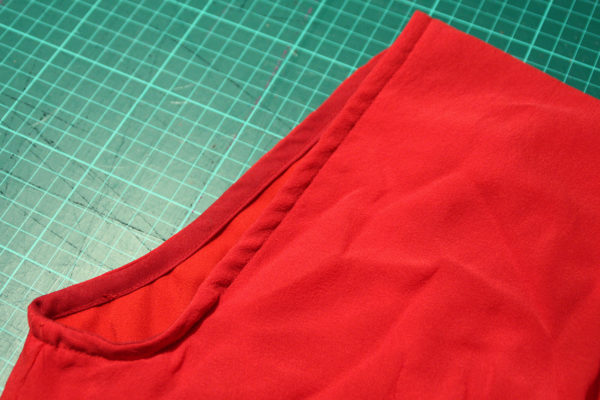
My button placket is interfaced with a lightweight shirt fusing. I wanted to make sure the placket had enough body to take the weight of the buttons without sagging and also make sewing the buttonholes stress free.
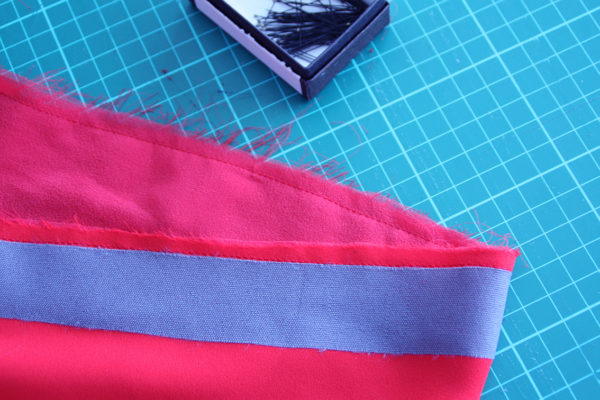
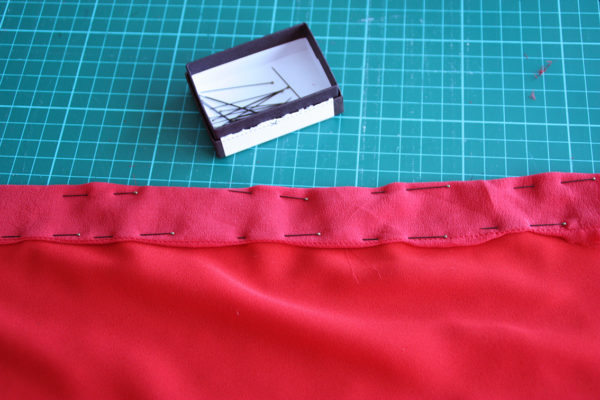
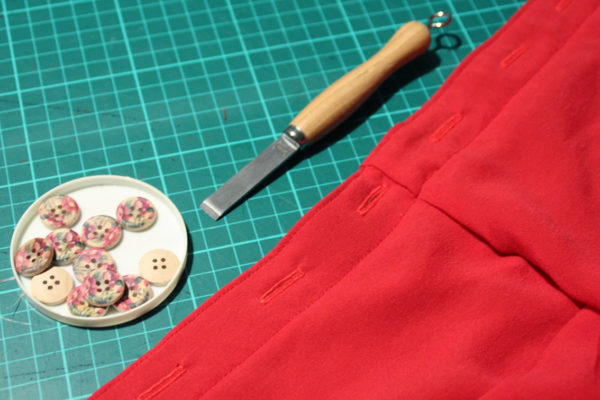
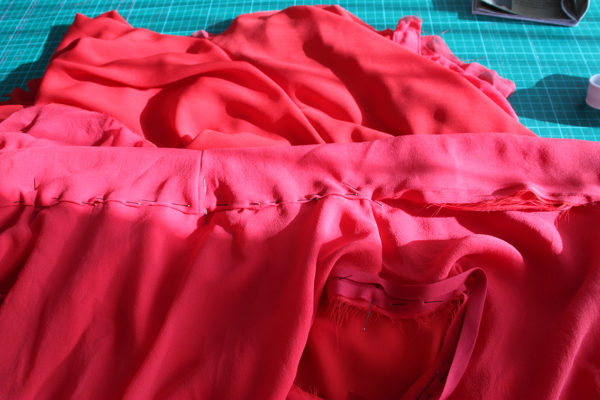
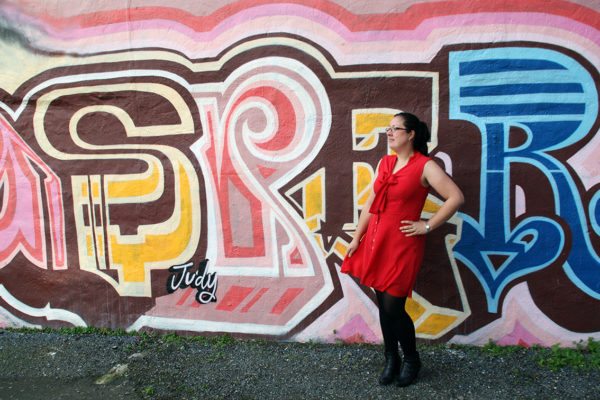
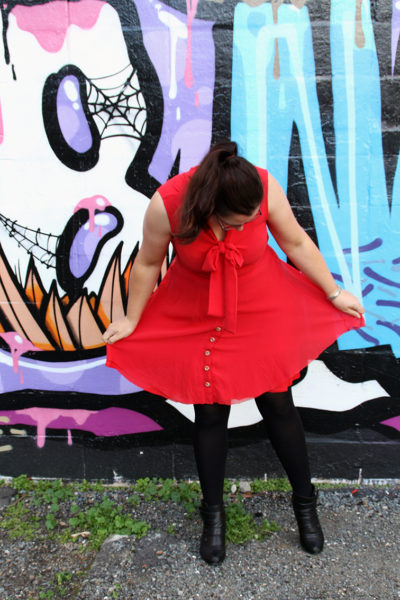
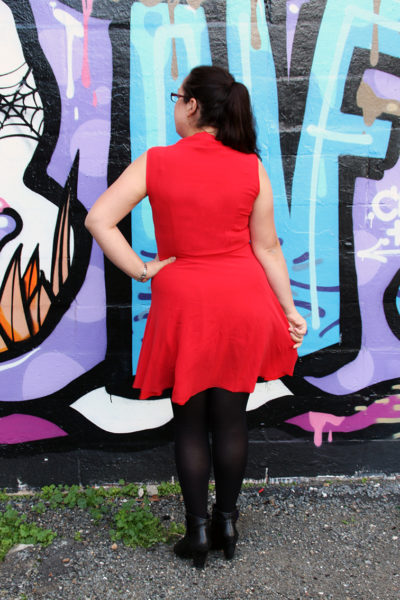
Happy sewing xx